福特CETP00.00-L-467实验室加速循环腐蚀试验标准
时间:2021-03-30 阅读:3525
1.0 introduction 介绍
1.1 TEST SCOPE 试验范围 上海鼎徵仪器仪表设备有限公司
This standard specifies an accelerated laboratory atmospheric corrosion test. The testing environment addressed is similar in effect to that of the salt load/ climatic part of the proving ground corrosion test procedure, CETP 00.00-R-343 and yields corresponding results. The objective of the test is to allow evaluation of the corrosion resistance of metals in environments where there is a significant influence of chloride ions, mainly as sodium chloride from a marine source or by winter road de-icing salt. The laboratory test provides full exposure to the salt load and humidity environment. It does not attempt to simulate other engraving factors such as mud loads, temperature stresses or wear. It serves as a general purpose atmospheric corrosion test and applies to a variety of materials, coatings, and interactions of materials, both as test specimens or in designed components. The test can be used as a design verification method in order to (a) develop and qualify new corrosion resistant products, (b) develop new pre-treatments and finishing processes, (c) select materials and, (d) perform quality control of the final product.
本标准是关于一项在实验室里加速进行的大气腐蚀试验。本文所述的试验环境类似于《试验场腐蚀试验程序CETP00.00-R-343》中的盐负荷/环境影响部分,得出相应的结果。试验目的在于评估金属在富含氯化物的环境中(主要是海水中的盐或冬天用于融雪的盐)的抗腐蚀性。该实验室试验主要是将试验件*暴露在湿润的盐负荷环境中,而非模拟其他摩擦因素如泥负荷、温度压力或磨损。该试验主要作为一项大气腐蚀试验,适用于各种各样的材料、涂层、试样或设计零部件材料的相互作用。该试验可作为一种验证设计的方法,用于(a)开发并验证新的抗腐蚀产品;(b)开发新的预处理和表面处理工艺;(c)选择材料;(d)对最终产品的质量控制。
The standard specifies controlled conditions for equipment and procedures to allow the test to be performed with a high degree of repeatability and reproducibility. It is designed to be suitable to run in various climate chambers, either as a fully automated procedure or with partial manual operations.
本标准说明了设备和程序的受控条件,让实验具有高度的重复性和再现性。本标准适用于多种环境试验箱,包括全自动试验或部分手动操作的试验。
1.2 SUMMARY OF TEST CONTENT 试验内容摘要
The workday test procedure consists of: 工作日的试验程序由以下几个方面组成:
A 6 h wet phase at room temperature. with intermittent exposure to salt solution (0.5% NaCl).
A 2.5 h transition phase with drying under climate control.
A 15.5 h phase with constant temperature and humidity (50°C, 70% RH).
室温下6小时的加湿阶段,间歇曝露到0.5%的氯化钠溶液中
2.5小时的过渡阶段,通过环境控制进行烘干
15.5小时的恒温恒湿阶段(50°C, 70% RH)
After repeating this procedure Mon-Fri a 48 h weekend phase under continued constant climate control is added.
从周一到周五重复该试验程序后,在周末加入持续恒定环境控,进行48小时的试验。
1.3 COMMONALITY 共通性
This is a CONTROL TEST and can be used to qualify components throughout the world. The test may be conducted at any location having the necessary equipment and facilities. Proposed revisions to this procedure must be submitted per FAP03-179.
这是一项可验证世界上所有的零部件的控制试验,可在任何地方进行,只要具备所需的设备仪器。对本试验程序的修改建议必须按FAP03-179提交。
2.0 Instrumentation 仪器 上海鼎徵仪器仪表设备有限公司
The following elements are usually required to conduct the test procedure:
进行试验程序一般需要以下仪器:
2.1 Compressed, clean air of 4 - 6 bars for cleaning salt solution from spray nozzles, as a source for the renewal of chamber air and for humidification, supplied by spray humidifiers.
2.1 4-6 bar的干净的压缩空气,用于清理喷嘴上的盐溶液、箱内换气和喷雾加湿器进行加湿。
2.2 A low conductivity water supply (20 mS max) for humidification or evaporative spray humidifiers and for the preparation of salt solutions.
2.2 一根低导电率的供水管(至大20 mS),用于加湿或喷雾加湿器以及准备盐溶液。
2.3 A tank for preparation and storage of salt solution or, alternatively, a system for direct on-line mixing of water and saturated NaCl solution to the actual concentration (0.5 ± 0.05% by weight)
2.3 一个用于准备和存储盐溶液的水槽,或者一套直接在线按实际浓度(0.5 ± 0.05%,按重量)混合水和饱和氯化钠溶液的系统。
2.4 A conductivity meter with built-in temperature compensation for preparation and control of the 0.5% NaCl salt solution (conductivity: 8.3 mS/cm + 0.80 at 20°C). A 0.50% by weight NaCl solution is used as a calibration standard at each measurement.
2.4 一个带内置温度补偿的电导仪,用于准备和控制0.5%的氯化钠盐溶液(温度为20°C时的导电性:8.3 mS/cm + 0.80)。 一份按重量为0.50%的氯化钠溶液,作为每次测量时的校正标准。
2.5 A high quality device for independent control of temperature and relative humidity shall be accessible. This instrument shall on a stipulated regular interval (Ref 5.4) be used for independent monitoring and calibration of the conditions in the very test plane of the exposure chamber. The total measurement error must not exceed 0.1°C.
2.5 一套高质量的设备,用于独立控制温度和相对湿度。该设备按照规定的时间间隔(参考5.4),独立监控和校正试验箱李的试验平面上的各项条件,测量总误差不超过0.1°C。
2.6 Racks of inert material for support and aligned fixation of test specimens must not hamper a free air-flow around the test objects, nor collect standing wetness. The test objects in a rack must not screen one another from the salt solution downfall and they should be exposed with the stipulated exposure angle to the spray (15- 20 degrees inclination from vertical).
2.6 由惰性材料制成的夹具,用于支撑、排列和固定试样,但不得妨碍试样周围的空气流通,不得累积水分。夹具上的试样不得相互遮蔽导致盐溶液淋不到试样上。试样应按规定的角度曝露到喷雾中(偏离垂直线15-20度)。
2.7 Pressurized hand-spray equipment for application of the 0.5% NaCl solution if a manual spray procedure is used. The capacity must be sufficient to meet the downfall requirement (Ref. 3.3.1).
2.7 如需采取手动喷洒,应使用适用于0.5%盐溶液的加压型手动喷雾器,喷雾器的容量必须能满足喷洒要求(见3.3.1)。
2.8 Funnels, beakers/ measuring glasses and a balance with at least 0.1 g accuracy for monitoring and calibration of salt solution downfall throughout the test plane of the exposure chamber.
2.8 漏斗、烧杯/量杯以及精度至少为0.1g的天平,用于监控和校准曝露箱中试验平面上落下的盐溶液。
2.9 All test measurement equipment must be calibrated and maintained per FAP03-015, Control, Calibration, and Maintenance of Measurement and Test Equipment.
2.9 所有试验的测量设备的校准和维护必须按照《FAP03-015测量和试验设备的控制,校准和维护程序》。
2.10 All applicable safety guidelines and procedures must be followed.
2.10 试验须遵守所有适用的安全指引和安全程序。
3.0 Equipment and facilities 设备设施 上海鼎徵仪器仪表设备有限公司
The necessary, permanently installed facility to conduct the test consists of a programmable humidity chamber of good quality. It is preferably equipped with an integrated rig for spraying salt solution of the required amount and accuracy, cooling capacity and a good internal circulation system for the conditioned air (Fig. 1). The exposure chamber shall be designed so that the test conditions described in the subsequent paragraphs can be obtained, controlled, and monitored during the test.
试验所需的安装的设施包括一个可编程的高质量湿度箱。湿度箱中建议能配备一套喷量准确度高的综合性盐雾喷洒装置、冷却装置和一套性能良好的空气内循环系统(如图1)。曝露箱应按要求设计,以使下文所述的试验过程中的各项条件能在得到满足、控制和监控。
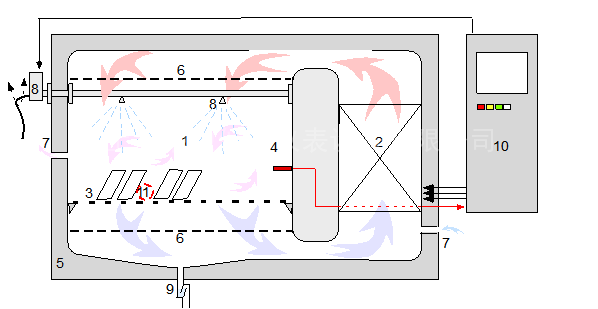
Fig. 1 Schematic view of a climate chamber equipped with functions suited for performance of the described test procedure: 1. Chamber test space, 2. Climatization unit, including fan, heating, cooling and humidification, 3. Test plane with samples, 4. Temperature/ humidity sensor for regulation, 5. Insulated walls/ lids, 6. Diffusors for improved air distribution, 7. Fresh air inlet/ "bleed", 8. Rain rig with nozzles and motor for swaying mode, 9. Gutter, 10. Control/ steering/ recording unit, 11. Position for monitoring/ calibration of climate with independent temperature/ humidity sensor.
图1 环境试验箱的图示,配备了进行本文所述的试验程序所需的功能:1. 试验空间;2. 环境系统,包括风扇、加热器、冷却器和加湿器;3. 放置试样的平面;4. 温湿传感器(调节用);5. 隔热壁/盖; 6. 空气扩散器(改善空气分布);7. 新鲜空气进气口; 8. 带喷头和摇摆模式驱动马达的喷洒器;9. 排水口;10. 控制/操作/记录系统;11. 带独立温室感应器的环境监控/校正位置。
3.1 CLIMATE CONTROL 环境控制
The humidity and temperature levels of the chamber during the test cycle shall be continuously monitored. The sensors should reflect the climate conditions in the test "plane" (Fig. 1, item 4). The mean value of the constant temperature/ relative humidity climate conditions must be within ±0.4°C and ±2% relative humidity (RH) respectively vs. the real, set value, i.e. these are the max tolerable mean offsets caused by the sum of calibration errors. At annual calibration this degree of accuracy must be fulfilled for the following three constant conditions: 25°C, 95% RH, 50°C, 95% RH and 50°C, 70% RH. At bimonthly control, during normal operation, this accuracy should be fulfilled at the constant climate conditions (50°C, 70% RH) during a work-day cycle.
试验过程中应连续不断地监控试验箱的湿度和温度水平。传感器会反映试验“平面”上的环境(如图1中第4项)。恒定温度/相对湿度的均值必须在±0.4°C范围内,相对湿度(RH)在±2%,分别对应实际值、设定值,这些就是由于累积的校正误差造成的平均偏移值的最大允许范围。 在年度校正过程中,这一精度必须得到满足,以保证以下三项恒定条件:25°C, 95% RH, 50°C, 95% RH以及50°C, 70% RH。在进行两月一次的正常控制时,工作日循环中的恒定环境条件(50°C, 70% RH)应能到达这一精度。
The maximum allowed short-term fluctuations in relative humidity overlaid on the calibrated mean value is ±3% RH, which implies a maximum allowed short-term temperature fluctuation of ± 0.6°C. Figure 2 is exemplifying the requirement on relative humidity.
叠加到校正平均值的相对湿度短期波动至大范围是±3% RH。这意味着短期温度波动的至大范围只能是± 0.6°C。图2举例说明了相对湿度的要求。
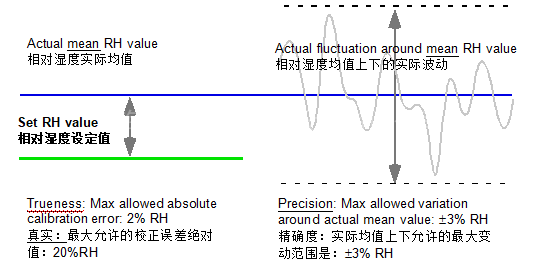
Fig. 2 Accuracy requirement on humidity deviations from set value
图2 湿度偏差离设定值的精度要求
The chamber controlling software/ hardware must be designed so that the relative humidity may be changed linearly with time as depicted in the illustrated test conditions, see Figure 5. In the 2-stage ramping from a wet chamber at 25 ±2°C to humid conditions at 50°C, 70% RH, the first heating stage to 40°C should be reached within 30 minutes without sample drying, which is secured by a nominal relative humidity setting to 95% RH. The second 2 h ramp must reach the stipulated final 50°C, 70% RH at the end of the ramp.
控制试验箱的软件/硬件必须设计成能使相对湿度随时间呈线性变化,如图5所示。从试验箱温度为25 ±2°C的湿润状态到50°C, 70% RH的湿润状态需经过两个阶段。一阶段应通过将相对湿度读数设定到95%RH,以保证温度在30分钟内达到40°C而试样不干燥。第二阶段为两小时,必须在结束前达到规定的50°C, 70% RH。
NOTE: For each new exposure situation this condition must be verified by an independent monitoring device (paragraph 2.5) with the sensor positioned among the actual test objects in their actual average plane of exposure (Fig. 1 Item 11). For monitoring : Deploy the sensor directly after the last spray event of the work-day wet phase.
注意:每次曝露的条件必须经过独立监控设备验证(见第2.5段),也就是实际试验物体所在的曝露平面之间的传感器(如图1,第11项)。在工作日湿润阶段的最后一次喷洒后直接调节传感器来进行监控。
In automated testing, forced cooling is necessary when proceeding from 50°C, 70 % RH controlled, constant conditions to macro-wet conditions at 25°C. The chamber must achieve a cooling from 50°C to 30°C within 30 minutes with the targeted 25°C met within 1 hour. If spraying is applied manually, then cooling the samples by letting the chamber be open with test objects kept wet may provide an option that does not require the use of a built-in cooling unit. It must be verified by temperature monitoring that cooling requirements are fulfilled under such conditions for the actual chamber type and test specimen load.
在自动试验过程中,要使试验箱从受控恒定条件50°C, 70 % RH变化到25°C下非常湿的条件,需要进行强制冷却。试验箱必须在30分钟内从50°C冷却到30°C,然后在1小时内到达目标温度25°C。如果是手动喷洒,可以打开试验箱同时让试样保持湿润,这样就不必使用内置冷却系统。在这种条件下要满足该类试验箱和试样负荷的冷却要求,必须通过温度监控保证。
3.2 RECOMMENDATIONS ON TEST CHAMBER FUNCTIONALITY
关于试验箱功能的建议
In order to meet the temperature and humidity accuracy requirements throughout the test area, the chamber should be equipped with means to provide well distributed circulation of conditioned air (meaning a local air velocity of at least a few cm/s over all parts of the test area, - Fig. 1 is exemplifying such a condition). Sufficient insulation of the chamber walls and lids is required in order to avoid excessive condensation on these surfaces. The more efficient air circulation, the less insulation is required.
- 为了在整个试验过程中满足温度和湿度的精度要求,试验箱应配备能使经调节温湿度、空气流动性好的装置(试验区域内各部分的内部气流速度至少是若干厘米/秒-例如图1。)试验箱的四壁和盖板要求得到有效隔热,以避免这些表面出现过渡冷凝。空气流动性越好,隔热需求越少。
Wall heating should be avoided, due to that heating by radiation tends to keep test object close to the chamber walls locally too dry to be within humidity specification (or a screen shall be installed to avoid such an effect). Provided the internal air circulation is efficient, wall heating is not required. The chamber air must be continuously renewed by a purge of not less than
1 m3/ h per m2 of test area (exemplified by Fig. 1, Item 7). This to assure that the CO2-level is not significantly depleted under any exposure conditions. Fresh air can be added dry from a compressed source or taken from ambient conditions, unless significantly polluted (> 50 ppb SO2).
由于热量辐射会使靠近箱壁的试样过度干燥,达不到湿度要求,因此应尽量避免试验箱壁受热(或者添加遮挡板来避免受热)。如果内部空气流动良好,就不必进行箱壁加热。应配备1 m3/ h每m2的空气净化器使试验区域内的空气不断更新(例如图1第7项)。这是为了保持CO2水平,避免其在曝露条件下被耗尽。干燥的新鲜空气可以由压缩机提供,或使用室内的空气(除非空气被严重污染(> 50 ppb SO2))。
3.3 EXPOSURE TO SALT SOLUTION 曝露到盐溶液中
3.3.1 For a fully automated procedure , the chamber shall be equipped with a spray device capable of producing a finely distributed, uniform spray falling on the test objects. The most reliable way of receiving a fairly uniform downfall is by installing a moving spray device, like the swaying rail with overlapping nozzles, depicted in Fig. 3. The spraying device shall be made of corrosion resistance materials. Plastic is recommended.
3.3.1 对于全自动的试验,试验箱内应配备喷洒装置,能使溶液得到妥善分配,均匀喷洒到试样上。能有效使溶液均匀喷洒的方法是安装一套可移动的喷洒装置,如带交叉喷头的摇摆轨道,如图3所示。喷洒装置应由耐腐蚀材料制成,建议是塑料。
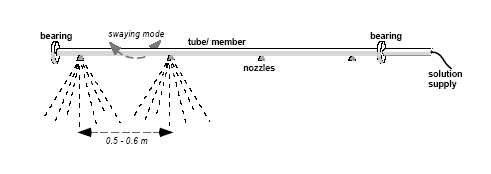
Fig. 3 Example of spray rig for obtaining uniform salt solution downfall.
图3 使盐溶液均匀喷洒的喷洒装置示例
A target average precipitation rate distributed over the workday 6 h wet period of this test procedure period is 5 L/m2, and shall not exceed 10 L/m2. For any local position the total precipitation over the 6 h period must not be lower than 3 L/m2 and not exceed 15 L/m2. Suggested nozzles type: Spraying Systems Uni Jet 800050VP. Mount the nozzles on a supporting tube 50-60 cm apart and about 1 m above the test objects. The nozzles shall be adjusted so that the fan plumes are in line with the tube/ supporting rail. An individual filter at each nozzle is strongly recommended to avoid any contaminations in the tiny slots. These low-cost plastic nozzles have a reliable function, but must be inspected in microscope at delivery in order to discard such with defect slot cuts. Stainless nozzles, even in 316 alloy, will be impaired by corrosion under the actual test conditions. Atomizing salt-spray nozzles should not be used, since they generate a too low precipitation rate to give sufficient leaching effect on the test objects. Achieving a uniform downfall with these types of nozzles can be difficult.
在本试验的工作日的6小时加湿阶段,平均喷洒密度的目标值为5 L/m2,且不能超过10 L/m2。在6小时周期内,箱内任何位置的喷洒密度都必须不低于3 L/m2,不高于15 L/m2。建议喷头类型:Uni Jet 800050VP喷洒装置。将喷头装在支承管上,相隔56-60cm,处于试样上方1米左右。调整喷头,使扇叶与支承管/支承轨成一直线。强烈建议在给每个喷头装上过滤器,以避免小槽中的污染物。虽然这些喷头价格低廉、功能可靠,但是发货时还须经过显微镜检验,以淘汰那些小槽切割不良的喷头。不锈钢喷头,就算是用316合金制成的,在也会在实际试验条件下受到腐蚀而损坏。雾化盐雾喷头喷洒密度过低,无法为试样起到有效的过滤作用,故不宜使用。这几类喷头喷洒都不均匀。
3.3.2 An automated spray-rig is allowed to be separated from the humidity chamber, i.e. the test objects are moved between two units on a work-day basis.
3.3.2 自动喷洒装置可从加湿箱中拆出来。也就是说,试样在一个工作日内在两套设备之间移动。
3.3.3 If there is no possibility to use an automated device for spraying, a manual spraying of the test object is allowed, either in or outside the test cabinet, provided: 1. The minimum precipitation rate of 5 L/m2 per 6 h wet session is fulfilled, 2. The spraying events are distributed over the 6 h period, so that the test object are kept constantly wet, and 3. The temperature requirement is fulfilled.
3.3.3 如果不能采用自动喷洒装置,可采用手动喷洒,在箱内箱外皆可,条件是:1. 在6小时加湿阶段完成前,喷洒密度至少为5 L/m2。2. 喷洒将分布在6小时周期内,以使试样保持湿润;并且;3. 保持要求的温度。
NOTE: Salt solution sprayed onto test objects must not be reused.
注意:喷洒到试样上的盐溶液不得重复使用。
4.0 Sample preparation 试样准备
Sample preparation before exposure, the sample orientation during exposure and the evaluation after exposure are usually stipulated in the engineering test standards addressing this test procedure.
曝露前试样准备,曝露期间的朝向和曝露后的评估方法一般会在本试验程序相关的工程试验标准中关于有所规定。
4.1 Painted and scribed panels: The test is optimized for exposing scribes in horizontal position on panels oriented to the angle stipulated in Paragraph 5.1.1. Scribe orientation has a similar effect on salt collection as the panel orientation. The scribe, or other type of damage, shall be positioned, so that a collecting area for precipitation is left above the exposed area of interest.
4.1 喷漆板和划线板:本试验已针对水平划线的板材按第5.1.1段所规定的角度朝向曝露进行了优化。划线的朝向的作用类似于板材朝向的盐聚集。划线或其他损伤都应定好位置,以便喷洒液收集区域位于目标曝露区域之上。
4.2 Component parts are to be in vehicle orientation position if at all possible. The salt solution spray should reach the areas of interest.
4.2 如果可能,零部件应尽量按照汽车朝向放置,并使盐溶液能淋到达目标区域。
4.3 Interested parties should agree on the location within the components where the corrosion is to be observed.
4.3 相关各方需商定零部件上将出现腐蚀的位置。
4.4 Interested parties should agree to any pre-conditioning, masking of edges, pre-testing, cleaning, or any other sample preparations.
4.4 相关各方需商定预处理、要遮盖的边缘、预测试、清洁或其他试样准备工作。
4.5 Interested parties should agree to any photographic details throughout the test and the areas to be examined and any assessments that are required.
4.5 相关各方需商定试验过程的具体细节、检测的区域以及要求的评估。
5.0 OPERATION 操作
5.1 BEFORE TEST START 试验开始之前
Prepare test objects according to the instructions in paragraph 4, which may include additional procedures, like preconditioning in other test equipments (e.g. heat treatment).
按照第4段的说明准备试样,也许将包括附加步骤,如在其他试验设备中进行预处理(比如热处理)。
5.1.1 Test object orientation: Components or test objects in the chamber shall be placed on/ mounted to non-corrosive surfaces in the appropriate agreed upon position. If the item is flat the test surface shall be within an 15-20° angle from vertical. Note that the inclination determines the amount of wetness collected on the panel and hence, the salt load when this film is subjected to climate control, which in turn influences the test result.
5.1.1 试样的朝向:试验箱中的零部件或试样应按照商定的朝向,放置或固定在防腐蚀的表面上。如果试样是平的,那么试验表面应在离垂直线15-20°角度范围内。请注意,板的倾角决定了溶液的收集量,从而影响试验片受环境控制时的盐负荷,进而影响试验结果。
5.1.2 Test object support: If it is necessary to suspend the objects, the material used shall be made of non-metallic inert materials. The test stands must not obstruct passing of air, nor disable proper drainage (The photo in fig. 4 shows an example of open well-drained supports for flat panels)
5.1.2 试样的夹具:如需将试样托起,夹具应采用非金属的惰性材料,而且不得阻碍空气流通或排水(图4就是一个开放且排水畅通的平板试样夹具)。
5.1.3 Test object exposure to salt spray: The component or test object shall be placed approximately 1 m from the spray heads if an automated spray rig is used. Flat samples in angled position must have their full horizontally projected surface exposed to spray collection (see drawing in fig. 4). This will also support a sufficient air circulation around the panels. Other test objects geometries than flat panels must obey these criteria as far as practically feasible.
5.1.3 试样曝露到盐雾中:如使用自动喷洒装置,零部件或试样应放置在离喷头1米左右的位置。按一定角度放置的平试样必须让其水平投影面*曝露到喷洒液体收集区域(见图4)。这还有助于板周围的空气流通。对于平板以外其他几何形状的试样,只要能实际操作,都必须遵循这些标准。
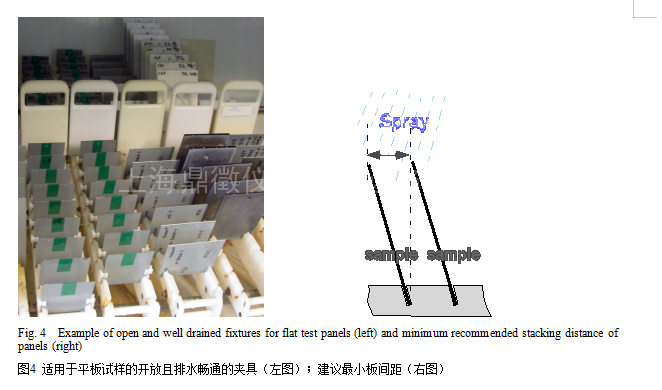
Fig. 4 Example of open and well drained fixtures for flat test panels (left) and minimum recommended stacking distance of panels (right)
图4 适用于平板试样的开放且排水畅通的夹具(左图);建议至小板间距(右图)
5.1.4 Duration of test: The number of test cycles shall be determined by the specification covering the component or object being tested. When not specified, the test period shall be agreed by the requester and the corrosion department.
5.1.4 试验持续时间:试验循环次数应由试样零部件或试样相关要求决定。如果没有要求,应由申请试验的一方和负责研究腐蚀的部门商定试验周期。
5.1.5 Control before test start: Run and monitor the test cycle at least a 24 h period before starting the test, provided not already in continuous operation.
5.1.5 试验开始前的控制:假如持续运行尚未开始,在试验开始之前先运行并监控试验循环至少24小时。
5.1.6 Start and end time of test: The test is only allowed to be started just before the first precipitation (Table I Step1A) in the weekly scheme, i.e. at the end of the "weekend" constant temperature/humidity phase. The test is ended at the end of the weekend humidity exposure.
5.1.6 试验的启动时间和结束时间:本试验只允许在一周计划中的一次喷洒(见表1,步骤1A)之前启动,即“周末”恒温恒湿阶段结束时。试验在周末加湿曝露阶段结束。
5.2 TEST EXPOSURE CONDITIONS 试验曝露条件
There are three basic exposure modes in the daily test scheme:
每日试验计划分三种基本曝露模式:
1. A continuous wet phase at 25± 2°C where the test objects are exposed to a 0.5% NaCl solution. The wet condition is maintained by intermittent spray exposure and with a temperature control without drying, or with the humidity control set high enough to not cause any practical drying.
1. 25± 2°C持续湿润阶段,在此阶段试样曝露到0.5%的氯化钠溶液中。通过间歇喷洒曝露和温度控制(不干燥),或调节湿度控制(足以防止物体干燥),试样的湿润状态得以保持。
2. A two-step transition from wet to controlled humidity climate.
2. 从湿润到受控湿度环境的两步过渡。
3. A period under constant temperature/ humidity control; 50 ± 0.6°C and 70 ± 3% RH. This is also the condition during weekend.
3. 恒温恒湿控制周期:50 ± 0.6°C,70 ± 3% RH。这也是周末的环境状态。
Table 1. Climate program, step by step in automated mode
表1 环境表,自动模式的各个步骤
Step 步骤 | Time elapsed 耗时 | Duration of step 步骤持续时间 | Climate settings at start of step 初始环境设定 | Comments 备注 | |||||||
no | h | m | h m | m | T (°C) | % RH | |||||
1a | 0 | 0 | 0 | 10* | 50* | 70* | Spray thoroughly 0.5% NaCl to wet and cool 0.5%氯化钠,湿透且冷却 | ||||
1b | 0 | 10 | 0 | 20 | 30-50 | Wet | Cool chamber with maximum capacity 最大限度冷却试验箱 | ||||
1a' | 0 | 30 | 0 | 3 | <30 | Wet | Spray to regain wetness (cooling dries) 通过喷洒使干冷的试验箱再次湿润 | ||||
1c | 0 | 33 | 2 | 27 | <30 | wet (95) | 25±2 to be reached within 1 h from start (1a) 从步骤1a开始,一小时内达到25±2 | ||||
1a' | 3 | 0 | 0 | 3 | 25±2 | wet | Secure and support wetness by spraying 通过喷洒保持湿润 | ||||
1c' | 3 | 3 | 2 | 54 | 25±2 | wet (95) | wet (95) = OK to set to 95% RH 湿度(95)= 可以设置到95%RH | ||||
1a' | 5 | 57 | 0 | 3 | 25±2 | wet | Defines wet condition before climate control 环境控制前明确湿工况 | ||||
2a | 6 | 0 | 0 | 30 | 25±2 | wet (95) | Start of quick temperature rise without drying 开始快速加温,但不能干燥 | ||||
2b | 6 | 30 | 2 | 00 | 40±0.61 | wet (95) | Start of slow drying by diffusion 通过扩散,开始缓慢干燥 | ||||
3a | 8 | 30 | 15 | 30 | 50±0.61 | 70±3 | Panels shall be free from visible wetness 板上无可见水迹 | ||||
3a | 24 | 00 | - | - | 50±0.61 | 70±3 | End of "workday" procedure “工作日”程序结束 | ||||
Repeat steps 1a - 3a another four times 步骤1a-3a再重复4次 | |||||||||||
3b | 120 | 00 | 48888 | 00 | 50±0.61 | 70±3 | Phase in with weekends in case of manual operations in "workday" procedure 假如“工作日”程序是手动操作,则在各个周末逐步进行 | ||||
3b | 168 | 00 | - | - | 50±0.61 | 70±3 | |||||
Repeat steps 1a-3b for required number of weeks 步骤1a-3b重复次数按各周要求 |
* Provided proceeding from step 3a or 3b 假如从3a或3b开始进行
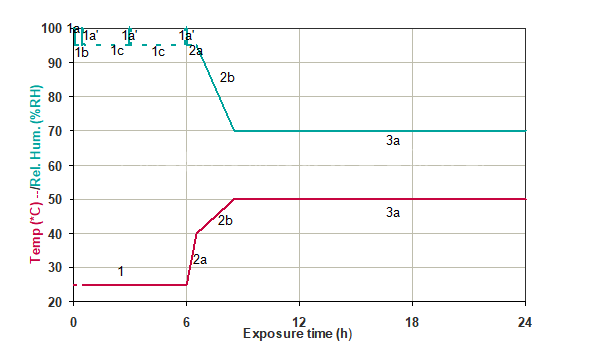
Fig. 5 Workday (Mon.-Fri.) test cycle 图5 工作日(一至五)试验循环
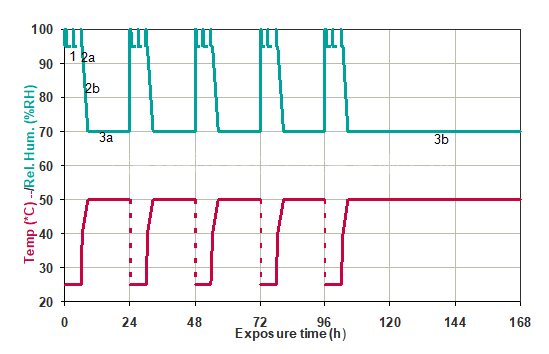
Fig. 6 Complete weekly program. 图6 完成每周计划
5.2.1 Operations within the wet phase at 25±2°C:
5.2.1 在25±2°C湿润阶段的操作
Exposure to 0.50±0.05% NaCl solution shall be performed at least in the beginning, middle and at the end of the 6 h wet phase.
在6小时湿润阶段的开始、中端和结束时至少各进行一次0.50±0.05%的氯化钠溶液曝露。
In automated mode, the first event may consist of a longer period of spray (1a - up to 10 minutes) in order to cool the samples and the chamber more efficiently from the 50°C, 70% RH condition. If all test operations are performed within the same climate chamber, it is essential to follow-up with efficient cooling after the first spray event, in order to reach a temperature below 30°C within the first 30 minutes of the wet phase (1b). After such cooling, which implies some drying, it is recommended to have another short spray event to assure that the solution on the panels have the stipulated concentration (1a' in Table 1/ Fig. 5) The final targeted temperature of 25±2°C shall be reached within the first hour.
在自动模式下,N1次喷洒时间会长一些(1a-10分钟),以使试样和试验箱从0°C, 70% RH的状态下更有效地冷却。如果所有试验操作都是在同一个试验箱中进行,N1次喷洒后的有效冷却非常重要,需要在湿润阶段(1b)的头30分钟内将温度降到30°C以下。冷却过后(意味着一定程度的干燥),建议进行一次短时间喷洒以保证板上的溶液达到规定的浓度(图5/表1中的1a)N1个小时内达到最终的目标温度25±2°C。
In an exposure case where the spray is applied manually into a stay-open chamber, or the samples are moved to another chamber or lab bench for spraying at wet phase exposure, cooling within the stipulated time is usually not a problem. Note that the spraying conditions described in 3.3.1 shall apply. During the remaining time of the wet phase (1c), the samples must not dry significantly. This is accomplished by securing that the temperature control is maintained without significant removal of humidified air. If the wet phase is performed in a trough on a bench or in an unheated chamber, it may be sufficient to just keep the panels in a closed volume between the spray events. In the fully integrated test condition, the climate control can be set to 25°C, 95% RH, which secures against any significant drying, without the risk of supplying humidity, which might occur if the humidity is set to e.g. 99% RH. The short spray event after approximately 3 h (1a') renews the wet film on the samples and secures against drying. The final spray event (1a') is to assure consistent starting conditions when entering the transition to controlled humidity climate.
假如是在敞开的试验箱里进行手动喷洒或者是将试样转移到其他试验箱或试验台上进行湿润阶段曝露,在规定时间内冷却一般不成问题。注意,应当按照第3.3.1段所述的喷洒条件进行。在湿润阶段(1c)剩余的时间里,不能让试样干燥。为保证这一点,可以保持温度而不大幅减少加湿空气。假如湿润阶段是在试验台上的水槽中进行,或者在未加热的试验箱中进行,仅仅在喷洒的间歇期间保持密封也许就足够了。在综合的试验条件下,环境控制可以设置成25°C, 95% RH。这样可以保证试样不干燥,毕竟当湿度设置为99%RH时加湿可能失效。大约3小时(1a’)后,需进行短时间喷洒以加强试样表面的保湿层,避免干燥。最后的喷洒(1a’)是为了在进入控制环境湿度的过渡阶段保证初始状态一致。
Note 1: The spraying scheme in Table 1 does not have to be literally followed, provided there is a spraying period at the beginning, middle and end of the 6-h wet period and the total amount of precipitation follows paragraph 3.3.1.
注意1:假如在6小时湿润阶段的开始、中段和结束各进行一次喷洒,而且喷洒总量符合第3.3.1段的要求,则不必逐一按照表1中的喷洒计划操作。
Note 2: Continuous spraying with atomizing salt-fog type nozzles is not an option.
注意2: 不得使用雾化盐雾喷头进行持续喷洒。
5.2.2 Transition to controlled humidity conditions:
5.2.2 过渡到受控湿润状态:
For both fully and partly programmable procedures, ramp up from 25°C and nominally set 95% RH to 40°C, 95% RH during 30 min, which means that wet conditions will prevail (2a). Slowly dry the wet corroding surfaces going from 40°C, and set 95% RH to 50°C, 70% RH for 2 h (2b). At the final controlled climate conditions there shall be no visible wetness on any corroding surface and the actual values must be within the set allowed limits. The reason for this two-step procedure with a quick temperature rise followed by slow drying at comparably high humidity is to favor drying by diffusion rather than drying by convection, since the latter varies considerably between different types of cabinets. Such variability is likely to have considerable impact on the test result.
对于*或部分可编制的程序,30分钟内从25°C,读数为95%RH,加温到40°C, 95% RH,意味着湿润状态会占上风(2a)。2小时内(2b)将湿润腐蚀的从40°C,95%RH,干燥到50°C, 70% RH。在最终控制的环境状态下,腐蚀表面不应再有水迹,而且实际数值必须在允许范围内。采取两步操作,即快速升温然后在相对较高的湿度下缓慢干燥,是因为在于扩散干燥比对流干燥好,后者在不同的试验箱里差别很大。这种差别有可能严重影响试验结果。
Note 3: The transitions 1b and 2a/b are essential to insure consistent test quality at the actual chamber specimen load. If the chamber humidity sensor is not positioned close to the samples, independent monitoring in the sample test plane should be accomplished according to section 3.1
注意3: 1b和2a/b的过渡对于保证试验质量的一致性是*的。如果试验箱内的湿度传感器并不靠近试样,根据3.1章节所述,应在试样测试平面上配备独立监控。
5.2.3 Constant climate conditions of 50°±0.6°C, 70±3% RH will prevail until a 24 h cycle is fulfilled, i.e. for 15.5 h. (3a) These constant exposure conditions are prolonged during "weekends", i.e. the last 48 h of the week cycle (3b) after finalizing the 5th "workday" cycle.
5.2.3 恒定状态50°±0.6°C, 70±3% RH将持续至24小时循环完成,即持续15.5小时(3a),而在“周末”计划中将持续更长时间:即完成第5个“工作日”循环后,周循环(3b)持续48小时。
5.3 AFTER EXPOSURE
5.3.1 Storage: For corroded samples of steel base or aluminum it is important to evaluate the samples no more than a week after finished test, if kept in ambient conditions. Otherwise test specimen should be kept in desiccators.
5.3 曝露后
5.3.1 保存:对于铁制或铝制腐蚀试样,如果保存在一般环境中,应在试验完成一周内进行对试样进行评估,否则应将试样保存在干燥器中。
5.4 QUALITY CONTROL
5.4.1 Workday control:
Check that the monitored temperature and humidity values are in accordance with set values.
5.4 质量控制
5.4.1 工作日控制:
检查确认温度值和湿度值符合设定值
5.4.2 Weekly control:
Check that the spray nozzles deliver the intended uniform spray pattern and that the spray rig works properly.
Check that the salt solution is within 0.50 + 0.05 % by wt. of NaCl solution, most conveniently with a conductivity meter (8.2 mS/cm). Use a reference standard solution. With the stipulated water quality (paragraph 2.2) pH is not subjected to control.
Check storage tanks and other supply sources.
5.4.2 周控制:
检查确认喷头能均匀喷洒,喷洒装置运转正常。
通过称量氯化钠溶液,检查确认盐溶液在0.50 + 0.05 %范围内,便捷的方法是使用电导仪(8.2 mS/cm)。使用参考标准溶液,规定的水质(见第2.2段)PH不受控制。
检查储存罐和其他供应源。
5.4.3 Bimonthly control:
Monitor the climate with an independent control device (paragraph 2.5) during test operation by placing the device in the chamber test plane just after the last spray of a wet phase and remove it before the first spray of the next wet event.
5.4.3 两月一次的控制:
在试验过程中使用独立控制设备监控环境(见第2.5段),即在LAST后一次湿润阶段喷洒过后将该设备放到箱里的试验平台上,然后在下一次加湿喷洒之前撤走。
5.4.4 Annual calibration:
Clean and service the complete equipment
Monitor the climate with an independent control device at the three different settings given in paragraph 3.1.
Check that the salt solution spray downfall is within specification. See Attachment 10.1
5.4.4 年度校正:
清洁并维修整套设备
在第3.1段所述的三个不同设定状态下,用独立控制设备监控环境
检查确认盐溶液的状态符合规定。见附件10.1。
5.5 DEVIATION HANDLING
5.5.1 Deviations, general: Any deviation during the test shall be recorded and its consequence on the test result shall be discussed with the test requester.
5.5 处理误差
5.5.1 一般误差:
试验过程中出现的任何误差都应记录下来,事后与试验申请方讨论误差对于试验结果的影响。
5.5.2 Test interruption: In case of a temporary chamber failure, an intended holiday stop or at annual service of the equipment: Store the test samples at room temperature (18-28°C) at 50-60% RH. for at most a week. This storage conditions will keep established corrosion cells at minimum activity without irreversibly quenching the corrosion activity, which may result from dry storage.
5.5.2 试验中断:
由于试验箱临时故障、节假日停机或对设备进行年度维修而中断试验:将试样储存在室温(18-28°C),相对湿度50-60% RH的环境下,最多一周。在这种储存条件下,已经生成的腐蚀细胞的活性可以控制在至低水平,而不会产生由于干燥储存形成的对腐蚀活性的不可逆抑制。
6.0 Acceptance Criteria
6.1 Acceptance Criteria is determined by the Corrosion Engineering Department of Ford Motor Company.
6.0 接收标准
6.1 接收标准由福特汽车公司腐蚀工程部决定。
7.0 presentation of data
7.1 Present all pertinent information agreed upon with requester. This may include number of cycles completed, pictures taken, special sample preparation, or positioning of the samples.
7.0 呈送数据
7.1 呈送与试验申请方商定的所有相关数据,包括完成的循环次数、照片特殊试样准备或试样位置。
8.0 references
8.1 CETP 00.00-R-343, Global 12-Week Total Vehicle Accelerated Corrosion Test.
8.2 FAP03-015, Control, Calibration, and Maintenance of Measurement and Test Equipment.
8.3 FAP03-179, Developing Corporate Engineering Test Procedures.
8.0 参考文件
8.1 CETP 00.00-R-343, 12周整车加速腐蚀试验
8.2 FAP03-015,测量与测试设备的控制,校正和维护
8.3 FAP03-179, 发展中企业工程试验程序
9.0 record of revisions
See metadata field "Review Note".
9.0 修改记录
见元数据版块“评审记录”
10.0 Attachment
10.0 附件
10.1 Recommended procedure for controlling of salt solution spray downfall
10.1 推荐关于盐溶液喷洒状况的控制程序
Check that the salt solution spray downfall is within specification by collecting the solution in a matrix of equally distanced beakers with defined collecting area. Cylindrical beakers of 6-10 cm diameter are recommended. They should be distanced with approximately 15 cm distance along the swaying tube/ rail throughout the whole test length, adjusted so that there is always a beaker directly under a nozzle and one just between two nozzles.
For a symmetrically positioned rain rig, three such rows of beakers are recommended; one under the tube/ rail, another parallel with the tube rail at either of the long-sides where the test area ends, and a third row in between these positions, which can have a reduced number of beakers, see example in Fig. 10.1:1. The collected amount of precipitation in each beaker during one 6 h wet period is measured using a 25-50 ml measuring glass.
通过在规定收集范围内按矩阵等距摆放收集溶液的烧杯,检查确认盐溶液喷洒状况符合要求。推荐使用直径为6-10cm的圆柱形烧杯。烧杯应沿着摇摆管/轨道摆放,贯穿整个试验长度。调整烧杯的摆放,使间距约为15cm,每个喷头下和两个喷头之间都各有一个烧杯。
对于对称型喷洒装置,建议将烧杯分三排摆放:一排放在管/轨道下面, 另一排放在试验箱的任意一侧长边缘,与管/轨道平行,第三排在前两排之间,烧杯数量可以少一些,见图10.1:1的示例。用一个25-50毫升的量杯测量一个6小时加湿周期内收集到的液量。
-
- Fig. 10.1:1 Example of positioning of beakers for collecting and controlling the salt solution spray downfall in a test plane
- 图10.1:1 烧杯放置示例,在试验平面内收集和控制喷洒下来的盐溶液