反应釜是一种用于化学反应的设备,在使用时需要注意以下诸多事项:
检查设备完整性:仔细检查反应釜的釜体、搅拌器、密封装置、阀门、仪表等各个部件是否完好,有无损坏、裂缝或泄漏的迹象。例如,查看釜体的材质是否有腐蚀的情况,搅拌桨的连接是否牢固等。
清洁工作:确保反应釜内部干净、无杂质残留。任何残留的杂质都可能影响化学反应的进行,甚至引发副反应。对于之前进行过不同反应的反应釜,需要进行清洗,有时还需要进行特殊的清洗程序,如使用特定的溶剂来清除顽固的残留物。
检查安全装置:确认安全阀、爆破片、紧急放空阀等安全装置能正常工作。安全阀需要设定在正确的压力值下开启,爆破片的额定压力也应符合要求,这些安全装置是防止反应釜内压力过高发生爆炸的关键措施。
校准仪表:对温度、压力、液位等仪表进行校准,保证其读数的准确性。因为这些参数对于控制反应过程至关重要,不准确的仪表读数可能导致反应失控。例如,如果温度仪表读数偏低,实际反应温度过高,可能会使反应剧烈,引发危险。
了解物料性质:在添加反应物之前,必须对反应物的性质(如腐蚀性、毒性、易燃性、氧化性等)有充分了解。针对不同性质的物料,采取相应的防护措施。比如,对于腐蚀性物料,要确保反应釜的材质能够耐受其腐蚀;对于易燃物料,要注意避免产生静电和火源。
控制加料速度和顺序:按照规定的加料速度和顺序添加物料。有些反应可能会因为加料速度过快而导致反应剧烈,产生大量的热或者气体,使反应釜内压力骤升。例如,在一些酸碱中和反应中,如果酸加入过快,可能会产生大量的热,引起溶液沸腾甚至冲出反应釜。对于有多种反应物的反应,加料顺序也很关键,否则可能无法得到预期的产物或者引发危险。
温度控制:严格监控反应温度,使其保持在设定的范围内。一般通过夹套或盘管内的热介质(如蒸汽、热水、热油)或冷介质(如冷水、冷冻盐水)来调节温度。对于放热反应,要及时移走反应产生的热量,防止温度过高;对于吸热反应,要提供足够的热量保证反应的持续进行。例如,在聚合反应中,温度过高可能会导致聚合物分子量分布过宽或者产生凝胶,影响产品质量。
压力控制:密切关注反应釜内的压力变化。如果压力超出正常范围,要及时采取措施,如调节进气量或出气量、降低反应温度等。压力过高可能会使反应釜破裂,引发严重的安全事故。例如,在有气体参与的反应中,气体的产生速度如果超过了排出速度,就会导致压力上升。
搅拌控制:确保搅拌器正常工作,保持适当的搅拌速度。搅拌的目的是使反应物充分混合,促进反应的均匀进行。如果搅拌不均匀,可能会导致局部反应物浓度过高,反应剧烈程度不同,影响反应的效率和产品质量。例如,在乳化反应中,搅拌速度不够可能会使乳液颗粒大小不均匀。
防止泄漏:定期检查反应釜的密封处,如釜盖与釜体的连接处、搅拌轴的密封处等,确保没有物料泄漏。泄漏的物料可能会对操作人员造成伤害,还可能污染环境。对于有毒或易燃的物料泄漏,后果更为严重。
防火防爆:如果反应涉及易燃、易爆物质,反应釜应在通风良好的环境中使用,远离火源和静电源。同时,严禁在反应釜附近吸烟或者进行可能产生火花的操作。例如,对于有机溶剂的反应,要确保反应区域的电气设备具有防爆功能。
个人防护:操作人员应穿戴适当的个人防护装备,如防护手套、护目镜、防护服等。这些防护装备可以在发生意外时,如物料飞溅、泄漏等,保护操作人员的安全。例如,在处理强酸碱物料时,防护手套和护目镜可以防止皮肤和眼睛受到伤害。
卸料安全:在反应结束后,卸料时要注意防止物料喷溅。如果反应釜内有压力,应先缓慢降压后再进行卸料操作。对于一些高粘度或者含有固体颗粒的物料,卸料可能会比较困难,需要采取适当的措施,如使用合适的卸料泵或者打开较大的卸料口。
设备清洗和维护:及时清洗反应釜,为下一次使用做好准备。清洗过程中同样要注意安全,避免残留的反应物对清洗人员造成伤害。在清洗后,对设备进行全面检查和维护,检查设备的磨损情况,更换损坏的部件,确保设备在下次使用时能够正常工作。
本厂闲置二手蒸汽加热反应釜
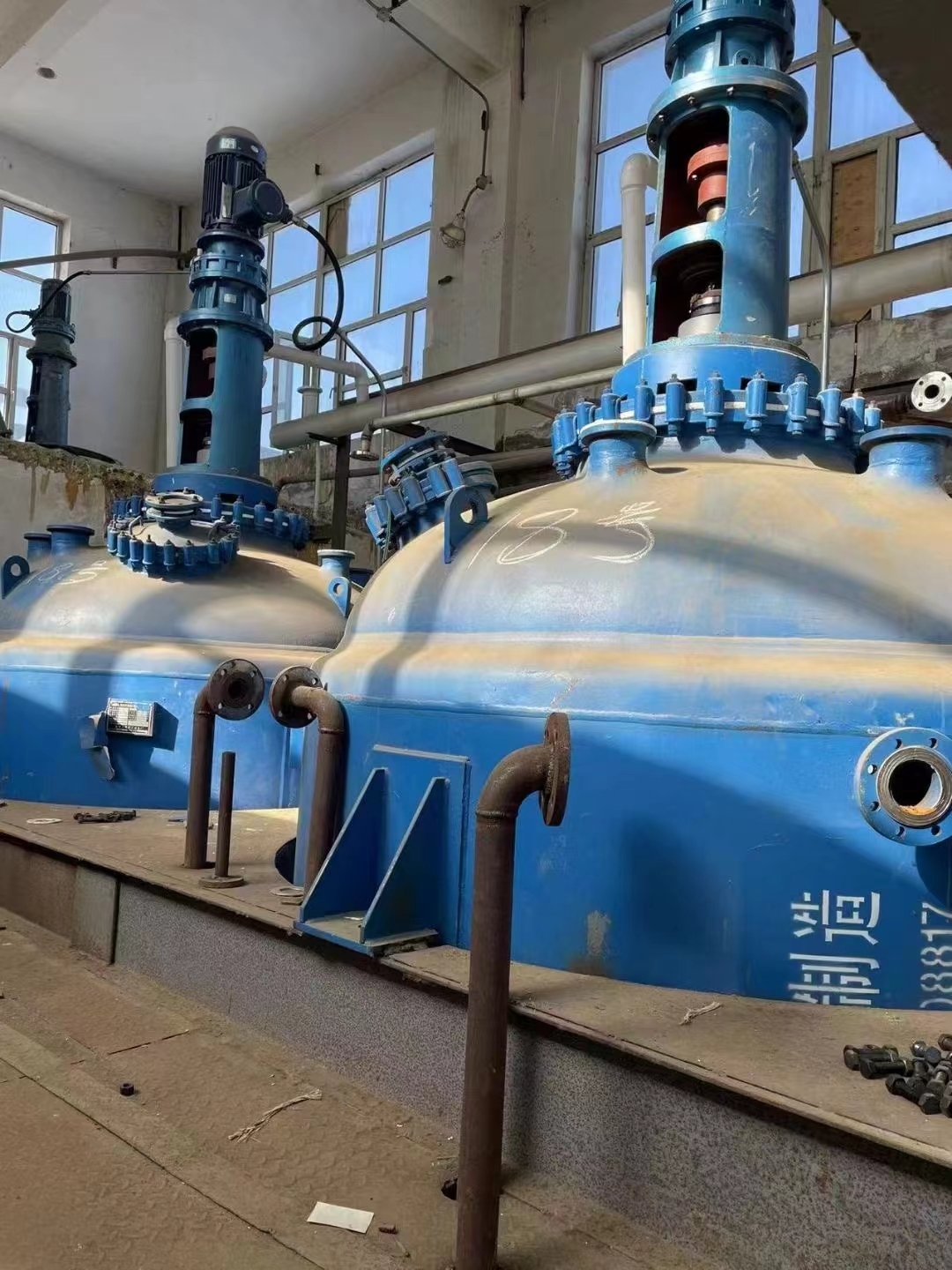
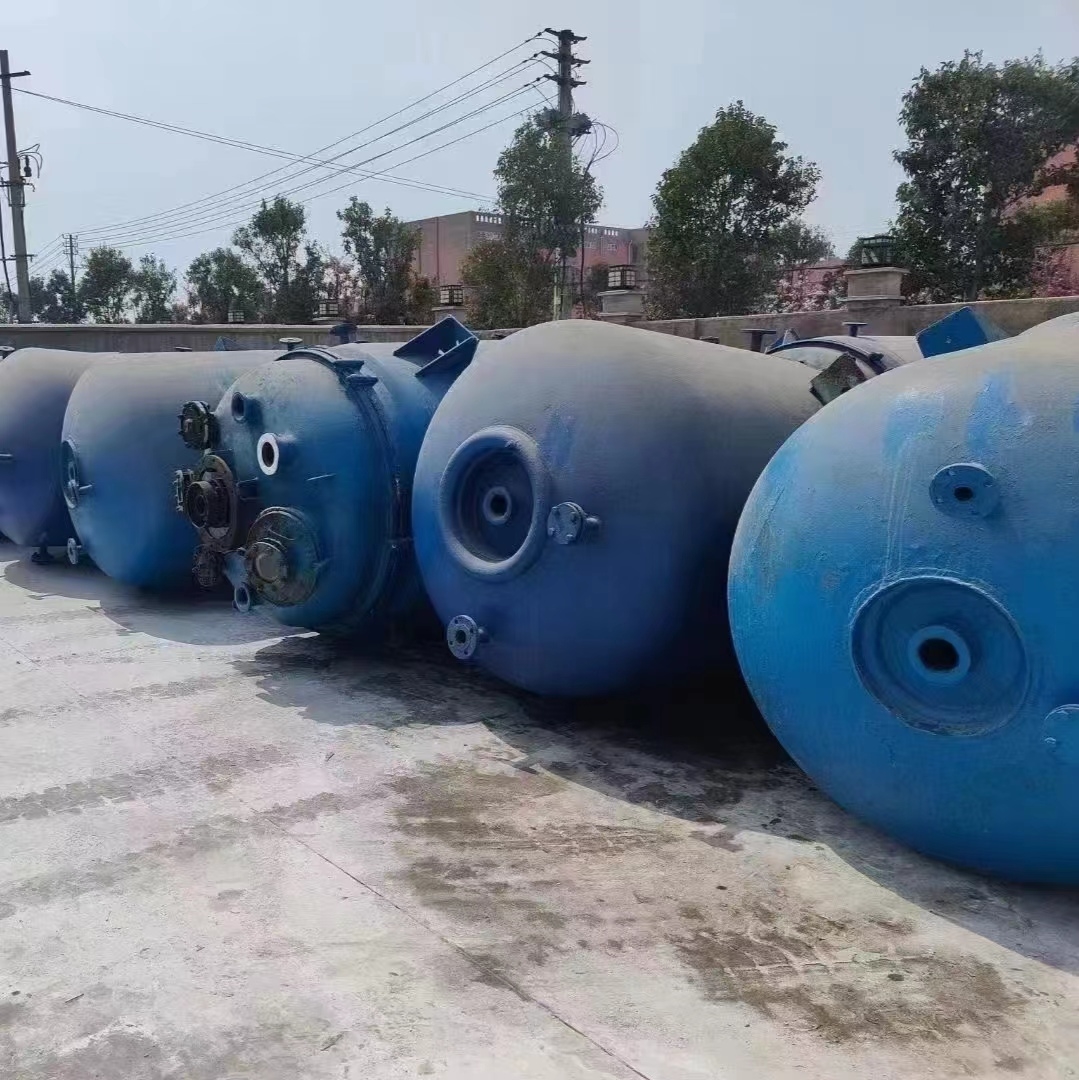
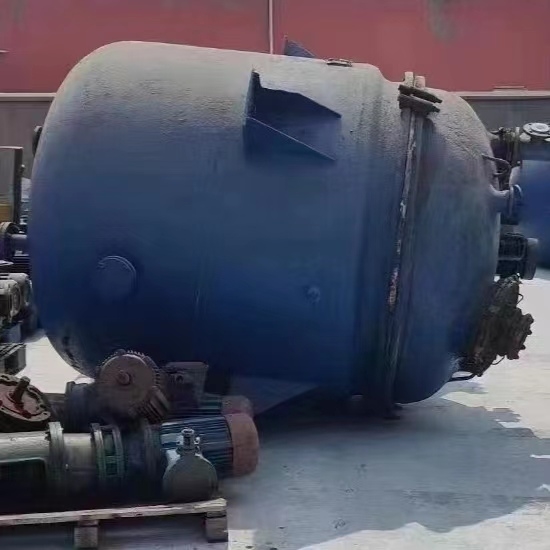
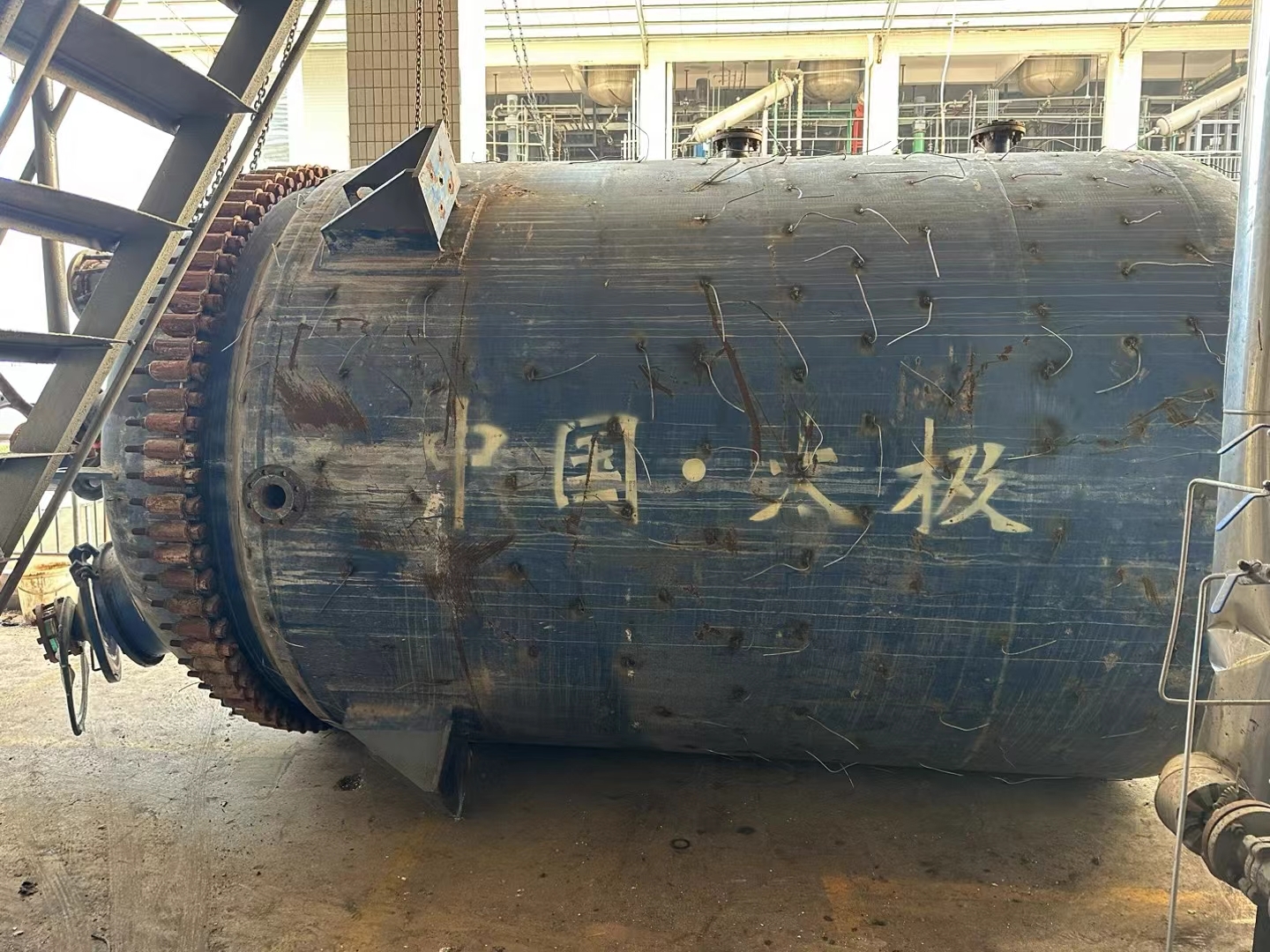
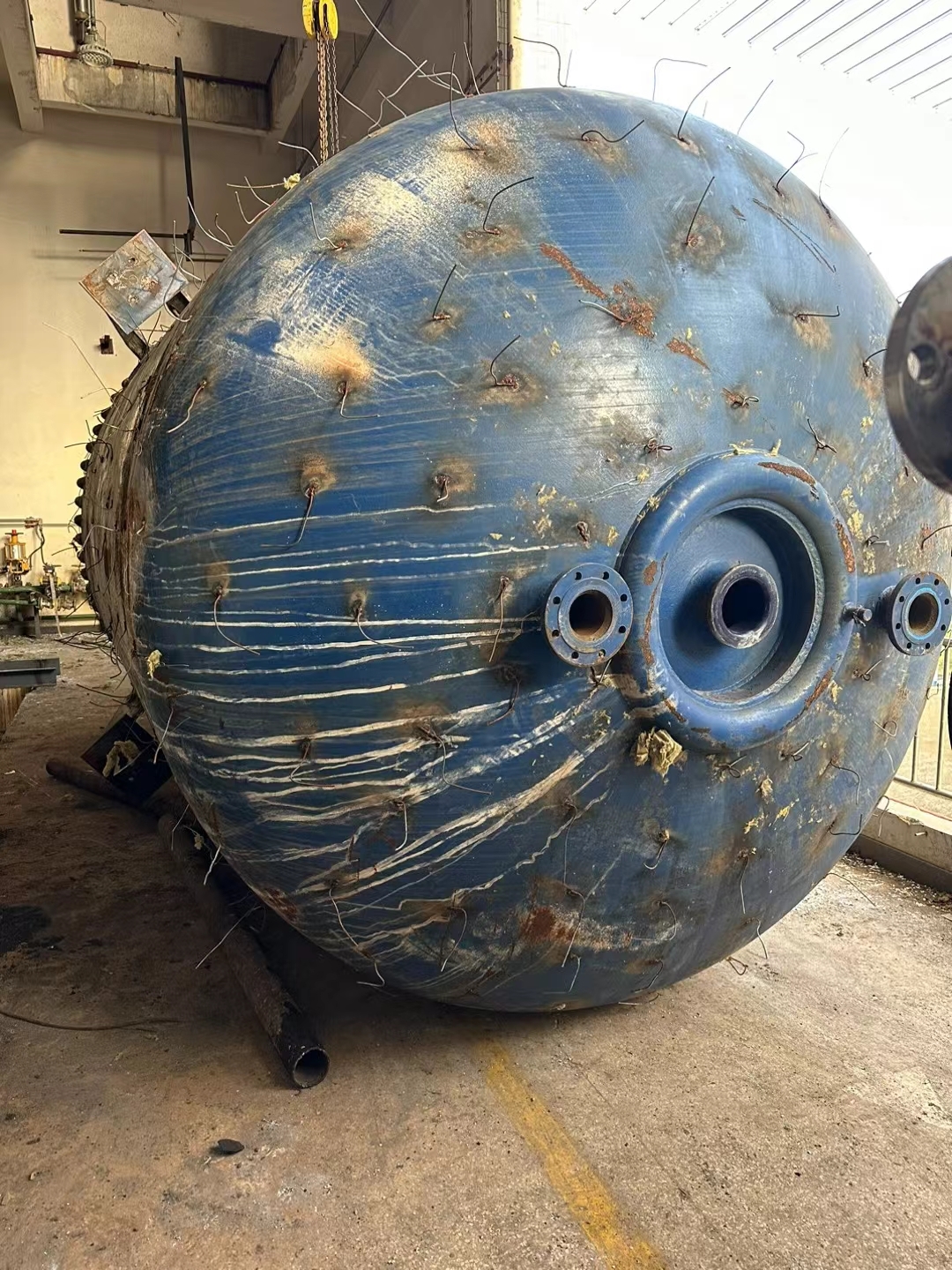