在工业生产中,错动折弯机的高效运行至关重要。当出现与错动相关的故障时,快速精准定位故障点成为关键,而这依赖于且完善的故障诊断系统。 基于传感器数据的实时监测
错动折弯机配备了多种传感器,如位移传感器、压力传感器、速度传感器等。这些传感器实时收集错动部件的运行数据,如错动位移、压力变化、运行速度等。例如,位移传感器能精确监测错动滑块的位置。一旦实际位移与预设值出现偏差,系统立即发出警报。通过对这些数据的实时分析,故障诊断系统可初步判断故障方向。若压力传感器显示压力异常升高,可能意味着错动部件间存在卡滞,需进一步排查相关部件。
故障树分析法的应用
故障树分析法是故障诊断系统的重要工具。它以错动故障现象为顶事件,将导致该故障的各种可能原因作为中间事件和底事件,构建逻辑树。例如,若错动精度超差为顶事件,中间事件可能包括模具磨损、导轨变形、控制系统故障等,底事件则细化到具体的零件损坏。通过这种层次化分析,系统能从复杂的故障现象中梳理出可能的故障路径,快速定位故障点。维修人员可依据故障树,从顶事件出发,逐步排查中间事件和底事件,缩小故障范围,提高故障定位效率。
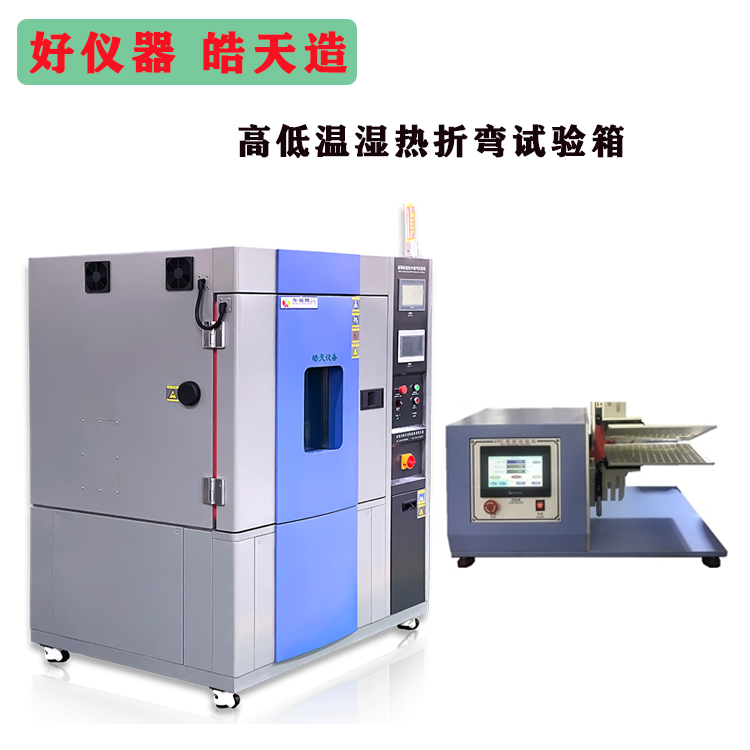
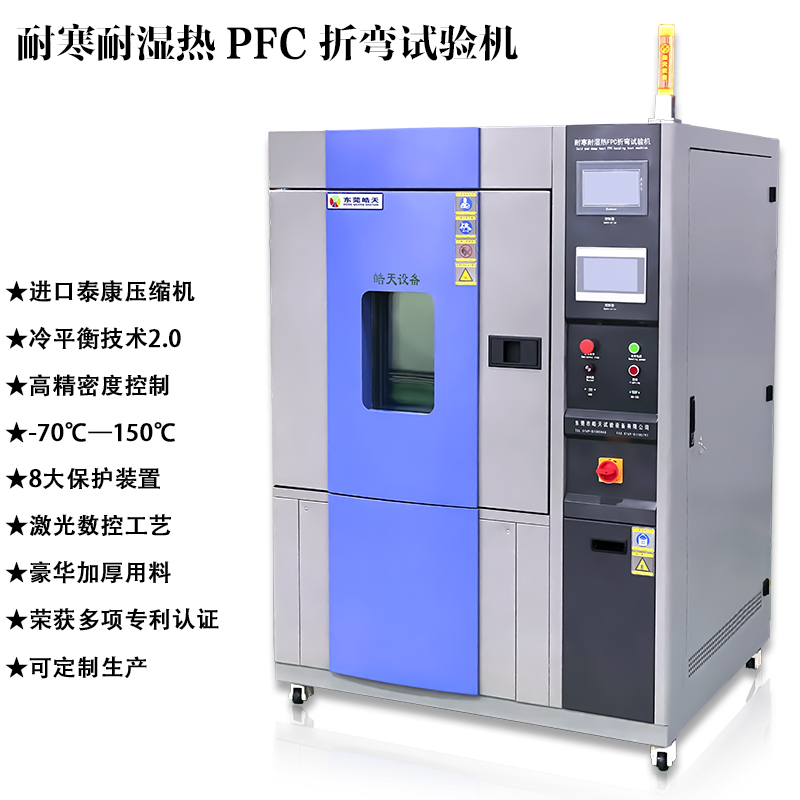
智能算法与机器学习助力故障诊断
现代故障诊断系统借助智能算法和机器学习技术,提升故障定位的准确性和速度。系统先收集大量正常与故障状态下的运行数据,以此训练神经网络等机器学习模型。当新的故障出现时,模型可通过对比当前数据与已学习的模式,快速判断故障类型及可能的故障点。例如,深度学习模型能自动提取数据中的特征,识别出细微的故障特征模式,即使是复杂或罕见的错动故障,也能准确判断。此外,智能算法还能对故障发展趋势进行预测,提前预警潜在故障,为维修维护争取时间。
历史故障数据与案例库的参考
故障诊断系统还建立了历史故障数据与案例库。当遇到新的错动故障时,系统可自动检索案例库,查找相似故障案例。这些案例记录了故障现象、原因分析及解决方法。若当前故障与历史案例相似,维修人员可直接参考解决方案,快速定位并解决问题。案例库不断更新完善,积累更多故障处理经验,进一步提高故障诊断系统的效率和准确性。
通过传感器实时监测、故障树分析、智能算法以及历史案例参考等多种技术手段,错动折弯机的故障诊断系统能够快速、准确地定位错动相关故障点,为设备的及时修复和高效运行提供有力保障。