分离机设备避免磨损和锈蚀可以从以下几个方面采取防范措施:
一、防止磨损的措施
正确的操作流程
物料处理:在进料时,要确保物料经过预处理,去除其中可能包含的硬质颗粒。例如,在处理含有固体杂质的液体物料时,可先通过滤网或沉淀等方式进行初步过滤。因为这些硬质颗粒在分离机高速旋转过程中,就像砂纸一样会不断摩擦转鼓和其他内部部件的表面,造成磨损。同时,要均匀地进料,避免物料冲击局部区域而导致局部过度磨损。
转速控制:严格按照设备说明书规定的转速范围运行。超速运转会极大地增加部件之间的摩擦力,而且离心力的异常增大可能使内部结构变形,加剧磨损。例如,转鼓在超速情况下,其与轴承的连接部位会承受远超设计标准的压力,使得轴承磨损加快。
运行时间管理:合理安排分离机的运行时间,避免长时间连续运行。长时间运行会使设备各部件处于持续的摩擦状态,热量积累也会影响部件的性能,进而加速磨损。根据任务和设备的性能,适当安排间歇时间,让设备有时间冷却和恢复。
良好的润滑措施
选择合适的润滑剂:根据分离机的工作环境和部件要求,选择具有适当粘度、抗磨损性能和化学稳定性的润滑剂。例如,在高温环境下工作的分离机,需要选择耐高温的润滑剂,以保证在高温下仍能有效减少摩擦。对于食品行业使用的分离机,要使用食品级润滑剂,防止润滑剂污染产品。
定期润滑:建立严格的润滑制度,按照规定的时间间隔和润滑点进行润滑。例如,对于分离机的轴承、齿轮等关键部件,应根据设备的运行时间和负荷情况,定期添加或更换润滑剂。一般来说,频繁使用的分离机可能需要每周或每月进行一次润滑检查和维护。
润滑方式优化:采用合适的润滑方式,如滴油润滑、油浴润滑或强制润滑等。对于高速旋转的部件,强制润滑系统能够更有效地将润滑剂输送到摩擦表面,保证润滑效果。同时,要确保润滑系统畅通无阻,定期检查润滑管道是否堵塞、油泵是否正常工作等。
定期维护和检查
部件检查:定期(如每周或每月,根据设备使用频率确定)对分离机的关键部件进行检查,包括转鼓、轴承、轴封等。查看部件表面是否有划痕、磨损痕迹等。例如,通过使用内窥镜等工具检查转鼓内部,及时发现微小的磨损点。对于磨损程度较轻的部件,可以采取修复措施,如对磨损的轴进行表面镀铬处理,恢复其尺寸精度。
平衡检查和校正:定期检查和校正分离机转鼓的平衡。转鼓不平衡会导致在运行过程中产生震动,这种震动会使部件之间的摩擦不均匀,加速磨损。可以使用专业的平衡检测设备,对转鼓进行动平衡和静平衡检测,发现不平衡时通过在合适的位置添加或去除配重的方式来校正。
更换易磨损部件:对于一些易磨损的部件,如密封件、轴承等,要根据其使用寿命和磨损情况及时更换。通常,密封件在出现轻微泄漏迹象时就应该考虑更换,轴承在运行时出现异常噪音、松动等情况时,应立即更换,以防止磨损进一步恶化。
二、防止锈蚀的措施
材料选择和表面处理
选用耐腐蚀材料:在分离机制造过程中,对于容易接触腐蚀性介质的部件,优先选用耐腐蚀的材料。例如,不锈钢材料在处理含有酸性或碱性液体任务中,具有良好的耐腐蚀性。对于一些特殊的腐蚀性环境,如在化工行业处理强腐蚀性的化学品,可能会选用哈氏合金等高级耐腐蚀材料制作关键部件。
表面涂层和镀层:对分离机的金属部件进行表面处理,如涂漆、镀锌、镀铬等。涂漆可以为部件提供一层物理屏障,防止外界腐蚀性介质与金属表面接触。镀锌和镀铬不仅可以起到防腐作用,还能在一定程度上提高部件的耐磨性。例如,分离机的外壳可以采用高质量的防腐漆进行喷涂,而一些内部的金属管道可以进行镀锌处理。
工作环境控制
控制湿度:保持分离机工作环境的相对湿度在合适的范围内。一般来说,相对湿度应控制在 40% - 60%。可以通过安装除湿设备来降低环境湿度,尤其是在潮湿的季节或潮湿的工作场所。高湿度环境会加速金属的锈蚀,因为空气中的水蒸气会在金属表面凝结,形成电解质溶液,引发电化学腐蚀。
避免腐蚀性物质接触:如果分离机周围存在腐蚀性气体或液体,要采取防护措施。例如,在化工车间使用分离机时,对于可能散发酸性气体的设备,要安装通风装置,将腐蚀性气体及时排出,防止其与分离机接触。对于可能溅到分离机上的腐蚀性液体,要设置防护挡板或围堰,并且在设备表面及时清理这些液体。
清洁和保养
及时清洁:在分离机使用后,及时清理表面的物料残留。因为有些物料可能含有腐蚀性成分,如含有盐分的液体。如果长时间附着在设备表面,会引发锈蚀。可以使用温和的清洁剂和柔软的抹布进行清洁,避免使用尖锐的工具刮擦设备表面。
保养剂使用:在清洁后,可以在设备表面涂抹适量的防锈保养剂。对于一些容易生锈的部位,如暴露在外的金属螺栓、螺母等,要重点涂抹。防锈保养剂可以在金属表面形成一层保护膜,延缓锈蚀的发生。同时,要定期检查保养剂的效果,根据需要及时重新涂抹。
大量二手管式分离机

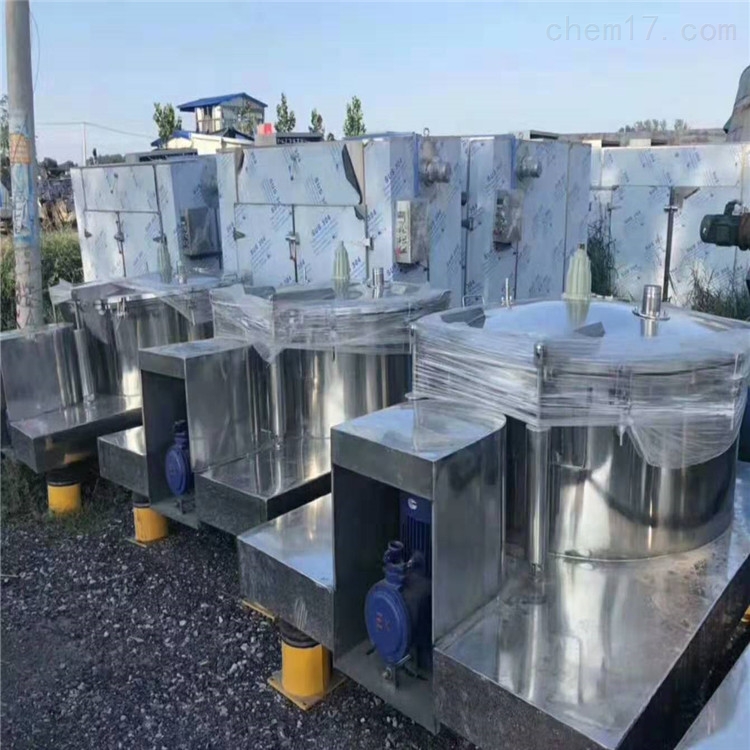
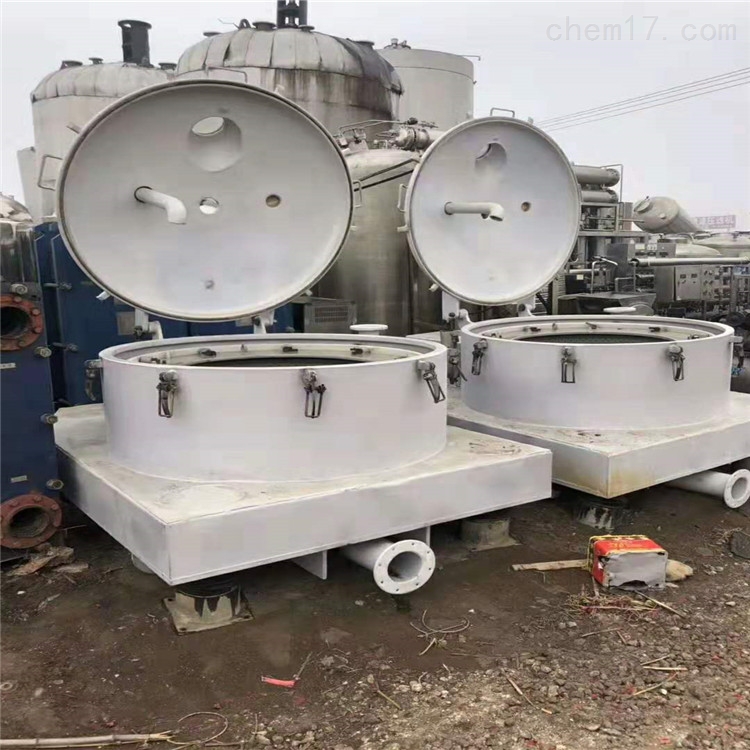

